Sensing and Visualizing Site Hazards
Advanced Safety System for Mine Utility Vehicles
Mine Safety Concerns
- Statistics: According to the Mine Safety and Health Administration (MSHA), about 40% of fatalities and over 30% of injuries at mine sites involve mobile equipment.
- Fatalities: In the last 5 years, 61 persons have died in accidents involving mobile equipment.
- Unique Challenges: The size and shape of mine and construction site equipment, coupled with the operator cab location, create unique blind areas.
- Blind Spots: These blind spots contribute to operators driving over highwalls or dump points, colliding with other equipment, and striking miners.
Despite these statistics from MSHA and NIOSH show that the industry suffers from a rising trend in fatalities between 2019 and 2023.
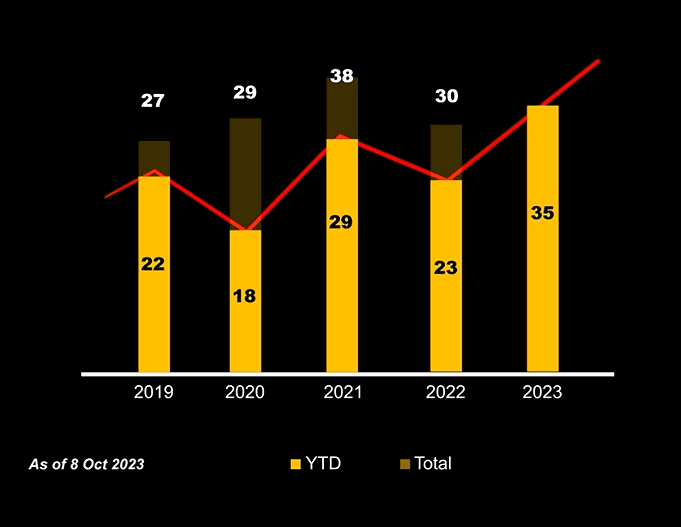
Blindspot Concerns At Mine Sites
At mine sites, the risk of accidents involving smaller vehicles is significantly high. These accidents often occur because smaller vehicles may lack adequate safety equipment and get crushed by larger vehicles with bigger blind spots.
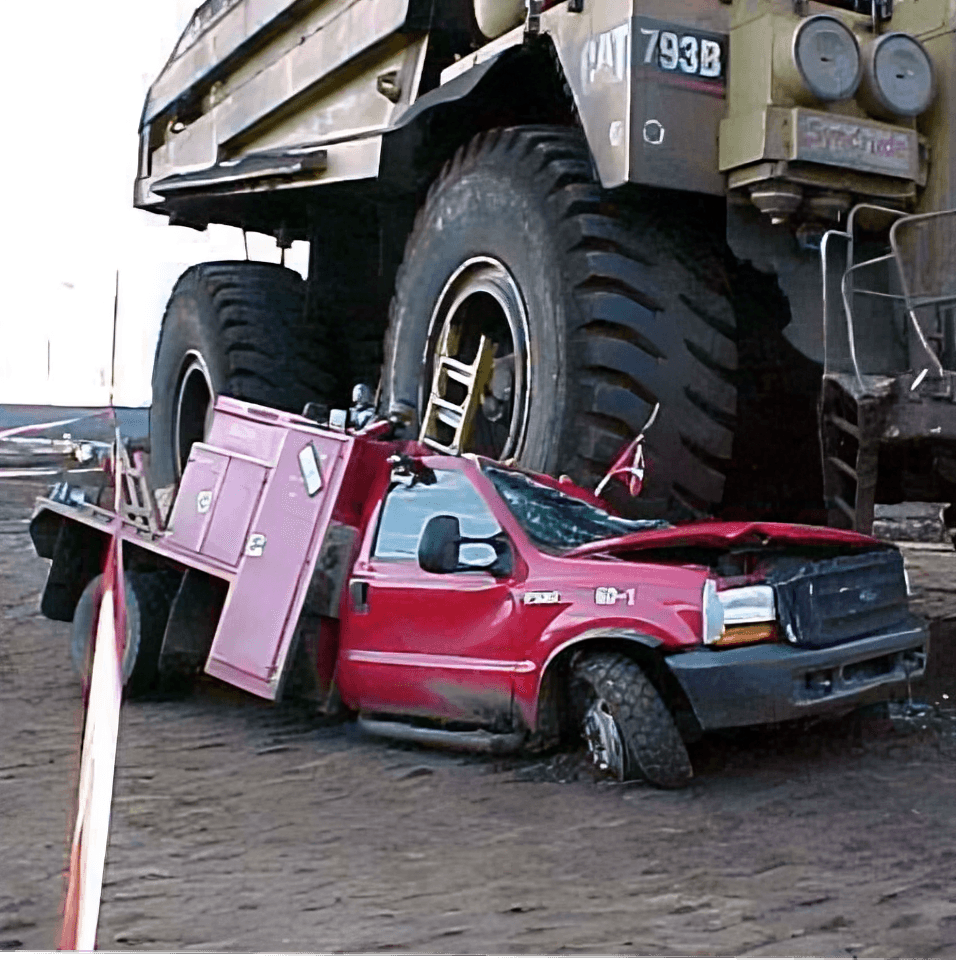
Accident due to Haul Truck Blind Spot
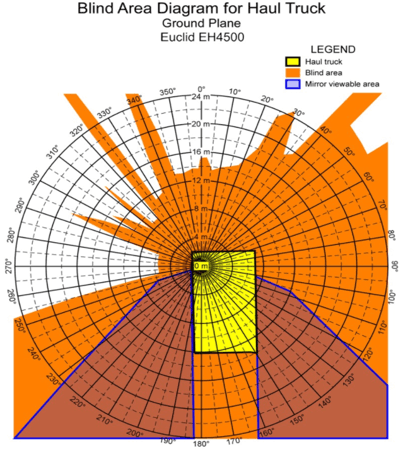
Blind Spots of a Haul Truck
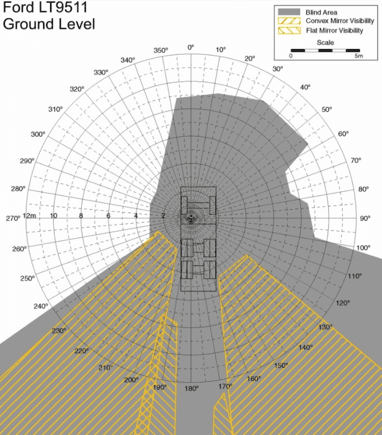
Blind Spots of an Small Vehicle (Ford)
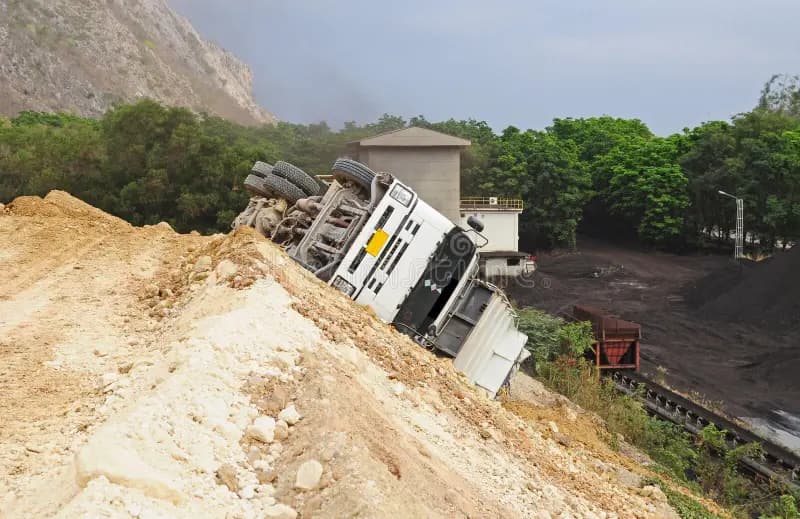
Haul Truck Crash on to Small Vehicle
Enhanced Communication
Comprehensive Training
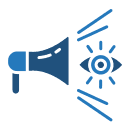
Visibility Aids
Collision Avoidance Technology
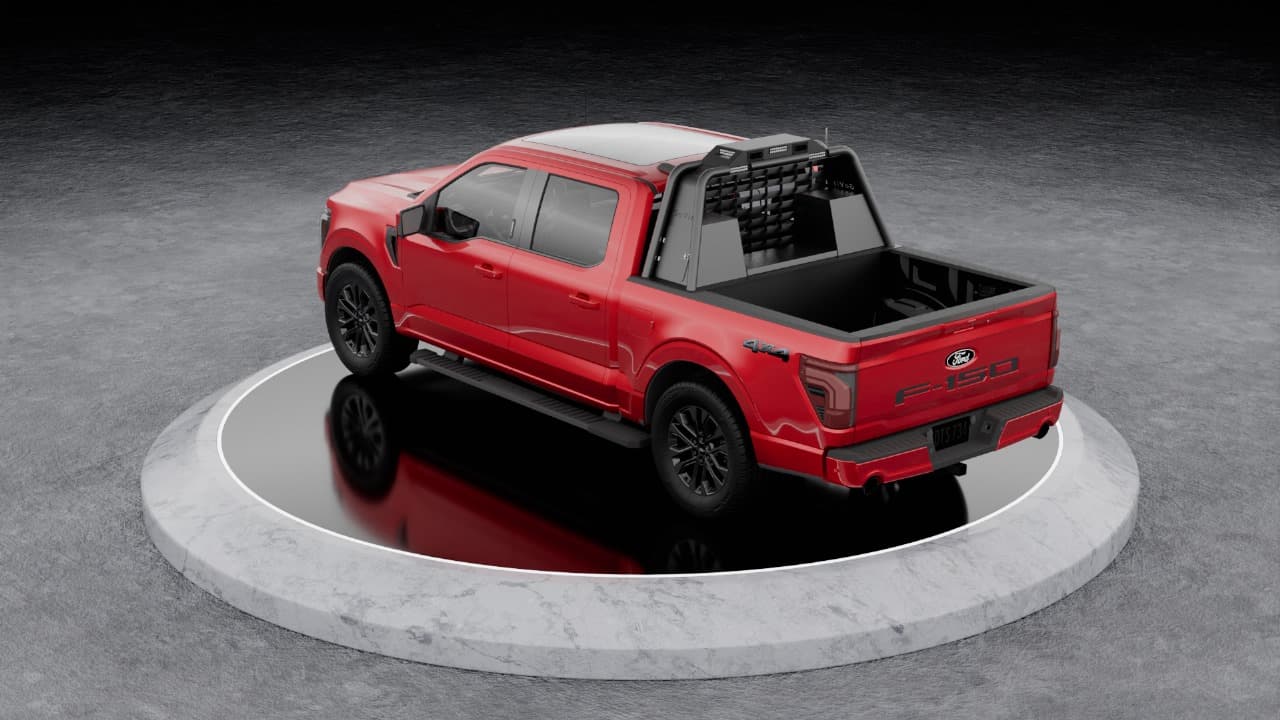
GoViz Headache Rack System
Goviz combines all the above measures in one affordable system. GoViz is an integrated headache rack that helps to mitigate hazards in mining, construction or outdoor recreational environments. The device is stacked with sensors that work to increase vehicle visibility, avoid collisions, and map hazardous conditions. It reduces accidents at the work site by alerting the vehicle operator of impending danger and informing others of hazards encountered on the site. Many other convenient features are packed in this innovative safety solution.
Excerpt From MSHA Final Rule
“After reviewing comments and relevant information, MSHA believes that structuring the final rule to include a performance-based requirement to identify and analyze hazards is more appropriate than a prescriptive requirement. The performance-based approach in the final rule allows operators the flexibility to devise and tailor a safety program that is appropriate for their specific and unique mining conditions and operations.”
Learn More from MSHA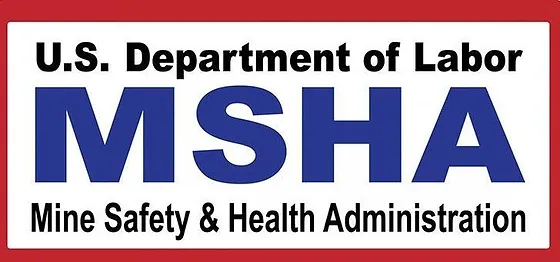
Four Major Areas of the Final Rule:
Identify and mitigate risks associated with surface mobile equipment operation.
Develop and maintain schedules for regular maintenance and repairs.
Assess new and existing technologies for potential safety enhancements at the mine.
Train miners to recognize and address hazards related to surface mobile equipment.